Once your products are 80% produced and packed, Pre-Shipment Inspection (PSI) in Indonesia is performed on-site by our quality inspectors. Based on a systematic protocol of units randomly selected from all batches of your order, it complies with statistical sampling procedures and industry standard processes to ensure that quality, quantity, packaging and labeling conform to your specifications and approved master samples.
However, you can specify when booking this service if you want 100% of the products to be ready and to be inspected. Every piece of product will be inspected and repacked and all defective goods will be sorted out.
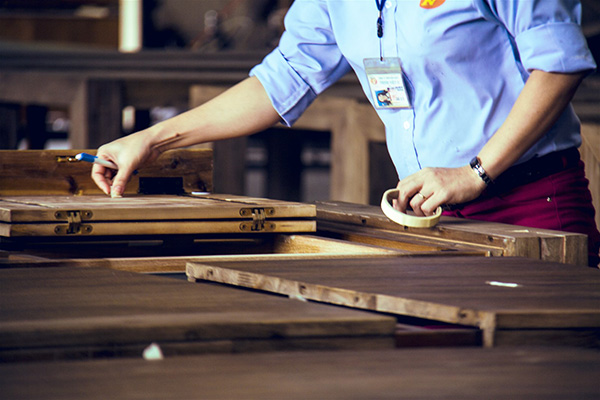
This is your final opportunity to take corrective actions before your production is finished and packed, and before you settle the balance payment.
What do we check during a Pre-Shipment Inspection?
- Status and quantity (ready, unpacked, still in production)
- Finished product comparison with master sample
- Product appearance and specifications (workmanship, color, dimensions, accessories, marking, weight, logo, etc.)
- Packaging appearance and specifications (printing, marking labels, dimensions, weight, thickness, etc.)
- On site test (functional test, abuse test, carton drop test, internal test, assembly check etc.)
- Any other special requirements you may have
What are the benefits of a Pre-Shipment Inspection?
Excellencial provides you third party quality control in Indonesia to check your products before the shipment and to help you to take the right decision with the correct information in hands. Our inspectors ensure that your order is complete and complies with your quality standards and specification requirements.
It is your last chance to refuse shipment before to pay the balance payment in order to avoid returns and protect your brand’s image.